مکینیکل سیلبہت سی مختلف صنعتوں کے لیے رساو سے بچنے میں بہت اہم کردار ادا کرتا ہے۔ سمندری صنعت میں موجود ہیں۔پمپ میکانی سیل، گھومنے والی شافٹ مکینیکل مہریں اور تیل اور گیس کی صنعت میں موجود ہیں۔کارتوس مکینیکل مہریں,مکینیکل مہریں یا خشک گیس مکینیکل مہریں تقسیم کریں۔ کار کی صنعتوں میں پانی کی مکینیکل مہریں ہوتی ہیں۔ اور کیمیائی صنعت میں مکسر مکینیکل مہریں (ایگیٹیٹر مکینیکل سیل) اور کمپریسر مکینیکل مہریں ہیں۔
مختلف استعمال کی حالت پر منحصر ہے، اسے مختلف مواد کے ساتھ مکینیکل سگ ماہی حل کی ضرورت ہوتی ہے۔ میں استعمال ہونے والے مواد کی بہت سی اقسام ہیں۔مکینیکل شافٹ مہریں جیسے سیرامک مکینیکل مہریں، کاربن مکینیکل مہریں، سلیکون کاربائیڈ مکینیکل مہریں,SSIC مکینیکل مہریں اورٹی سی مکینیکل سیل.
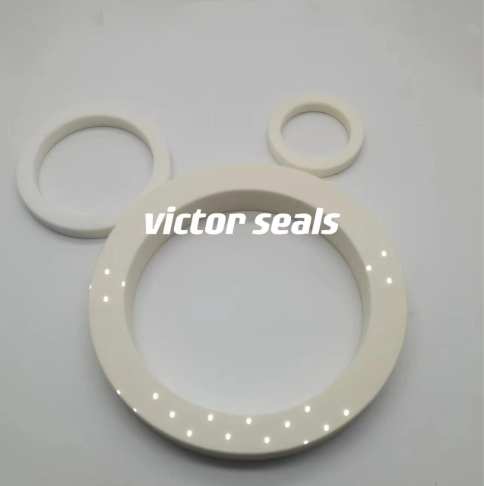
سیرامک مکینیکل سیل
سیرامک مکینیکل مہریں مختلف صنعتی ایپلی کیشنز میں اہم اجزاء ہیں، جو دو سطحوں، جیسے گھومنے والی شافٹ اور ایک اسٹیشنری ہاؤسنگ کے درمیان سیالوں کے رساو کو روکنے کے لیے ڈیزائن کی گئی ہیں۔ یہ مہریں ان کی غیر معمولی لباس مزاحمت، سنکنرن مزاحمت، اور انتہائی درجہ حرارت کو برداشت کرنے کی صلاحیت کے لیے انتہائی قابل قدر ہیں۔
سیرامک مکینیکل مہروں کا بنیادی کردار سیال کے نقصان یا آلودگی کو روک کر سامان کی سالمیت کو برقرار رکھنا ہے۔ وہ متعدد صنعتوں میں استعمال ہوتے ہیں، بشمول تیل اور گیس، کیمیائی پروسیسنگ، پانی کی صفائی، دواسازی، اور فوڈ پروسیسنگ۔ ان مہروں کے وسیع پیمانے پر استعمال کو ان کی پائیدار تعمیر سے منسوب کیا جا سکتا ہے۔ وہ اعلی درجے کی سیرامک مواد سے بنائے گئے ہیں جو دیگر سیل مواد کے مقابلے میں اعلی کارکردگی کی خصوصیات پیش کرتے ہیں.
سیرامک مکینیکل مہریں دو اہم اجزاء پر مشتمل ہوتی ہیں: ایک مکینیکل سٹیشنری چہرہ (عام طور پر سیرامک مواد سے بنا)، اور دوسرا مکینیکل روٹری چہرہ (عام طور پر کاربن گریفائٹ سے بنایا جاتا ہے)۔ سگ ماہی کی کارروائی اس وقت ہوتی ہے جب دونوں چہروں کو سپرنگ فورس کا استعمال کرتے ہوئے ایک ساتھ دبایا جاتا ہے، جس سے سیال کے اخراج کے خلاف ایک مؤثر رکاوٹ پیدا ہوتی ہے۔ جیسا کہ سامان چلتا ہے، سیل کرنے والی چہروں کے درمیان چکنا کرنے والی فلم سخت مہر کو برقرار رکھتے ہوئے رگڑ اور پہننے کو کم کرتی ہے۔
ایک اہم عنصر جو سیرامک مکینیکل مہروں کو دوسری اقسام سے الگ کرتا ہے وہ پہننے کے لیے ان کی شاندار مزاحمت ہے۔ سیرامک مواد بہترین سختی کی خصوصیات کے مالک ہیں جو انہیں بغیر کسی نقصان کے کھرچنے والی حالتوں کو برداشت کرنے کی اجازت دیتے ہیں۔ اس کے نتیجے میں دیرپا مہریں بنتی ہیں جنہیں نرم مواد سے بنائے گئے مہروں کے مقابلے میں کم بار بار تبدیل کرنے یا دیکھ بھال کی ضرورت ہوتی ہے۔
لباس مزاحمت کے علاوہ، سیرامکس غیر معمولی تھرمل استحکام کی بھی نمائش کرتے ہیں۔ وہ انحطاط کا سامنا کیے بغیر یا اپنی سگ ماہی کی کارکردگی کو کھوئے بغیر اعلی درجہ حرارت کا مقابلہ کر سکتے ہیں۔ یہ انہیں اعلی درجہ حرارت والے ایپلی کیشنز میں استعمال کے لیے موزوں بناتا ہے جہاں مہر کے دیگر مواد وقت سے پہلے ناکام ہو سکتے ہیں۔
آخر میں، سیرامک مکینیکل سیل بہترین کیمیائی مطابقت پیش کرتے ہیں، مختلف سنکنرن مادوں کے خلاف مزاحمت کے ساتھ۔ یہ انہیں ان صنعتوں کے لیے ایک پرکشش انتخاب بناتا ہے جو معمول کے مطابق سخت کیمیکلز اور جارحانہ سیالوں سے نمٹتی ہیں۔
سیرامک مکینیکل مہریں ضروری ہیں۔اجزاء کی مہریںصنعتی آلات میں سیال کے رساو کو روکنے کے لیے ڈیزائن کیا گیا ہے۔ ان کی منفرد خصوصیات، جیسے پہننے کی مزاحمت، تھرمل استحکام، اور کیمیائی مطابقت، انہیں متعدد صنعتوں میں مختلف ایپلی کیشنز کے لیے ترجیحی انتخاب بناتے ہیں۔
سیرامک جسمانی جائیداد | ||||
تکنیکی پیرامیٹر | یونٹ | 95% | 99% | 99.50% |
کثافت | g/cm3 | 3.7 | 3.88 | 3.9 |
سختی | ایچ آر اے | 85 | 88 | 90 |
پوروسیٹی کی شرح | % | 0.4 | 0.2 | 0.15 |
فریکچرل طاقت | ایم پی اے | 250 | 310 | 350 |
حرارت کی توسیع کا گتانک | 10(-6)/K | 5.5 | 5.3 | 5.2 |
تھرمل چالکتا | W/MK | 27.8 | 26.7 | 26 |
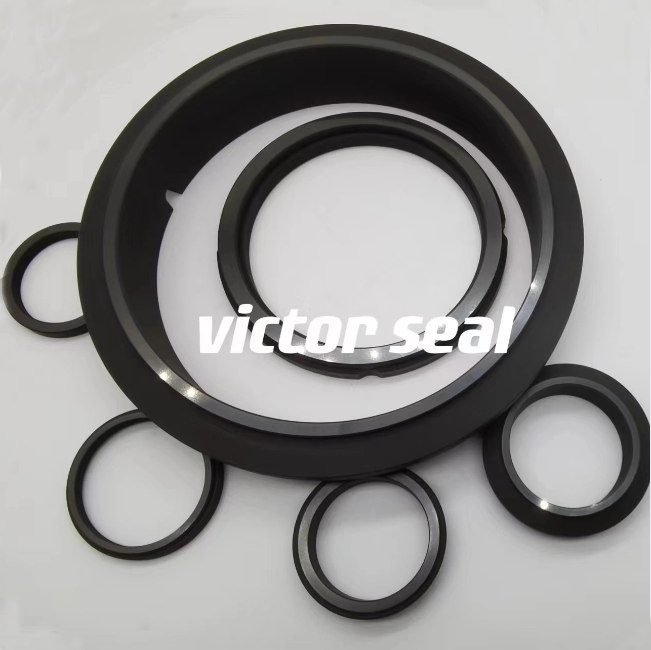
کاربن مکینیکل سیل
مکینیکل کاربن مہر کی ایک طویل تاریخ ہے۔ گریفائٹ عنصر کاربن کا ایک آئسفارم ہے۔ 1971 میں، ریاست ہائے متحدہ امریکہ نے کامیاب لچکدار گریفائٹ مکینیکل سگ ماہی مواد کا مطالعہ کیا، جس نے ایٹمی توانائی کے والو کے رساو کو حل کیا۔ گہری پروسیسنگ کے بعد، لچکدار گریفائٹ ایک بہترین سگ ماہی مواد بن جاتا ہے، جو سگ ماہی کے اجزاء کے اثر سے مختلف کاربن مکینیکل مہروں میں بنتا ہے۔ یہ کاربن مکینیکل مہریں کیمیکل، پیٹرولیم، الیکٹرک پاور انڈسٹریز جیسے ہائی درجہ حرارت سیال مہر میں استعمال ہوتی ہیں۔
چونکہ لچکدار گریفائٹ اعلی درجہ حرارت کے بعد پھیلے ہوئے گریفائٹ کے پھیلاؤ سے بنتا ہے، اس لیے لچکدار گریفائٹ میں باقی رہنے والے انٹرکلیٹنگ ایجنٹ کی مقدار بہت کم ہے، لیکن مکمل طور پر نہیں، اس لیے انٹرکلیشن ایجنٹ کے وجود اور ساخت کا مصنوعات کے معیار اور کارکردگی پر بہت زیادہ اثر پڑتا ہے۔
کاربن سیل چہرے کے مواد کا انتخاب
اصل موجد نے مرتکز سلفیورک ایسڈ کو آکسیڈینٹ اور انٹرکیلیٹنگ ایجنٹ کے طور پر استعمال کیا۔ تاہم، دھاتی جزو کی مہر پر لاگو ہونے کے بعد، لچکدار گریفائٹ میں سلفر کی تھوڑی سی مقدار باقی رہ گئی جو طویل مدتی استعمال کے بعد کانٹیکٹ میٹل کو خراب کرتی ہے۔ اس نکتے کو مدنظر رکھتے ہوئے، کچھ گھریلو اسکالرز نے اسے بہتر بنانے کی کوشش کی ہے، جیسے سونگ کیمن جنہوں نے سلفیورک ایسڈ کے بجائے ایسٹک ایسڈ اور آرگینک ایسڈ کا انتخاب کیا۔ تیزاب، نائٹرک ایسڈ میں سست، اور درجہ حرارت کو کمرے کے درجہ حرارت تک کم کرتا ہے، جو نائٹرک ایسڈ اور ایسٹک ایسڈ کے مرکب سے بنایا گیا ہے۔ نائٹرک ایسڈ اور ایسٹک ایسڈ کے مرکب کو داخل کرنے والے ایجنٹ کے طور پر استعمال کرتے ہوئے، گندھک سے پاک پھیلے ہوئے گریفائٹ کو پوٹاشیم پرمینگیٹ کے ساتھ آکسیڈینٹ کے طور پر تیار کیا گیا، اور ایسیٹک ایسڈ کو آہستہ آہستہ نائٹرک ایسڈ میں شامل کیا گیا۔ درجہ حرارت کو کمرے کے درجہ حرارت تک کم کیا جاتا ہے، اور نائٹرک ایسڈ اور ایسٹک ایسڈ کا مرکب بنایا جاتا ہے۔ پھر اس مکسچر میں قدرتی فلیک گریفائٹ اور پوٹاشیم پرمینگیٹ شامل کیے جاتے ہیں۔ مسلسل ہلچل کے تحت، درجہ حرارت 30 سینٹی گریڈ ہوتا ہے۔ 40 منٹ کے رد عمل کے بعد، پانی کو غیر جانبدار کرنے کے لیے دھویا جاتا ہے اور 50 ~ 60 سینٹی گریڈ پر خشک کیا جاتا ہے، اور بڑھا ہوا گریفائٹ اعلی درجہ حرارت کی توسیع کے بعد بنایا جاتا ہے۔ یہ طریقہ اس شرط کے تحت کوئی ولکنائزیشن حاصل نہیں کرتا ہے کہ پروڈکٹ توسیع کے ایک خاص حجم تک پہنچ سکے، تاکہ سگ ماہی مواد کی نسبتاً مستحکم نوعیت حاصل کی جا سکے۔
قسم | M106H | M120H | M106K | M120K | M106F | M120F | M106D | M120D | M254D |
برانڈ | رنگدار | رنگدار | رنگدار فینول | اینٹیمونی کاربن (A) | |||||
کثافت | 1.75 | 1.7 | 1.75 | 1.7 | 1.75 | 1.7 | 2.3 | 2.3 | 2.3 |
فریکچرل طاقت | 65 | 60 | 67 | 62 | 60 | 55 | 65 | 60 | 55 |
دبانے والی طاقت | 200 | 180 | 200 | 180 | 200 | 180 | 220 | 220 | 210 |
سختی | 85 | 80 | 90 | 85 | 85 | 80 | 90 | 90 | 65 |
پوروسیٹی | <1 | <1 | <1 | <1 | <1 | <1 | <1.5 | <1.5 | <1.5 |
درجہ حرارت | 250 | 250 | 250 | 250 | 250 | 250 | 400 | 400 | 450 |
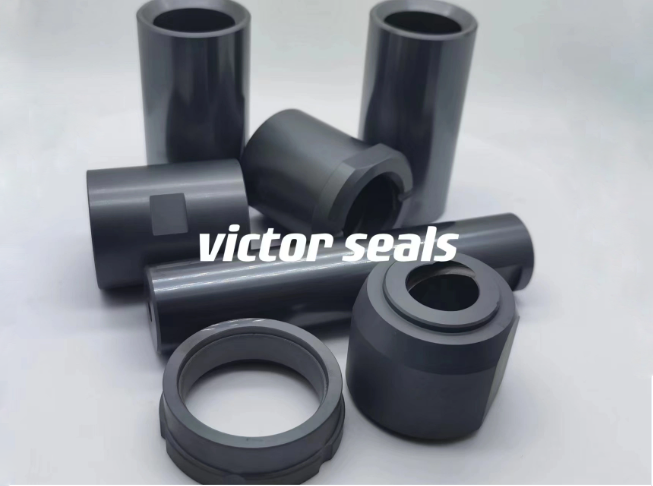
سلیکن کاربائیڈ مکینیکل سیل
سلیکون کاربائیڈ (SiC) کو کاربورنڈم کے نام سے بھی جانا جاتا ہے، جو کوارٹج ریت، پیٹرولیم کوک (یا کول کوک)، لکڑی کے چپس (جسے سبز سلکان کاربائیڈ تیار کرتے وقت شامل کرنے کی ضرورت ہوتی ہے) وغیرہ سے بنی ہوتی ہے۔ سلیکون کاربائیڈ میں بھی فطرت میں ایک نایاب معدنیات ہے، شہتوت۔ عصری C, N, B اور دیگر نان آکسائیڈ ہائی ٹکنالوجی ریفریکٹری خام مال میں، سلکان کاربائیڈ سب سے زیادہ استعمال شدہ اور اقتصادی مواد میں سے ایک ہے، جسے گولڈ اسٹیل ریت یا ریفریکٹری ریت کہا جا سکتا ہے۔ اس وقت، چین کی سلکان کاربائیڈ کی صنعتی پیداوار کو سیاہ سلکان کاربائیڈ اور سبز سلکان کاربائیڈ میں تقسیم کیا گیا ہے، یہ دونوں ہیکساگونل کرسٹل ہیں جن کا تناسب 3.20 ~ 3.25 اور مائکرو ہارڈنیس 2840 ~ 3320kg/m² ہے۔
سلیکن کاربائیڈ مصنوعات کو مختلف ایپلیکیشن ماحول کے مطابق کئی اقسام میں درجہ بندی کیا جاتا ہے۔ یہ عام طور پر زیادہ میکانکی طور پر استعمال ہوتا ہے۔ مثال کے طور پر، سلکان کاربائیڈ مکینیکل مہر کے لیے ایک مثالی مواد ہے کیونکہ اس کی اچھی کیمیائی سنکنرن مزاحمت، اعلی طاقت، اعلی سختی، اچھی لباس مزاحمت، چھوٹے رگڑ گتانک اور اعلی درجہ حرارت کی مزاحمت ہے۔
SIC مہر کی انگوٹھیوں کو جامد انگوٹی، موونگ رِنگ، فلیٹ انگوٹی وغیرہ میں تقسیم کیا جا سکتا ہے۔ SiC سلکان کو مختلف کاربائیڈ پروڈکٹس میں بنایا جا سکتا ہے، جیسے کہ سلکان کاربائیڈ روٹری رنگ، سلکان کاربائیڈ سٹیشنری سیٹ، سلکان کاربائیڈ بش وغیرہ، صارفین کی خصوصی ضروریات کے مطابق۔ یہ گریفائٹ مواد کے ساتھ مل کر بھی استعمال کیا جا سکتا ہے، اور اس کا رگڑ گتانک ایلومینا سیرامک اور سخت مرکب سے چھوٹا ہے، لہذا اسے اعلی پی وی ویلیو میں استعمال کیا جا سکتا ہے، خاص طور پر مضبوط تیزاب اور مضبوط الکلی کی حالت میں۔
SIC کا کم رگڑ اسے مکینیکل مہروں میں استعمال کرنے کے اہم فوائد میں سے ایک ہے۔ اس لیے SIC دوسرے مواد سے بہتر طور پر ٹوٹ پھوٹ کا مقابلہ کر سکتا ہے، جو مہر کی زندگی کو بڑھاتا ہے۔ مزید برآں، SIC کا کم رگڑ چکنا کرنے کی ضرورت کو کم کرتا ہے۔ پھسلن کی کمی آلودگی اور سنکنرن کے امکان کو کم کرتی ہے، کارکردگی اور وشوسنییتا کو بہتر بناتی ہے۔
SIC بھی پہننے کے لئے ایک عظیم مزاحمت ہے. اس سے ظاہر ہوتا ہے کہ یہ خراب یا ٹوٹے بغیر مسلسل استعمال کو برداشت کر سکتا ہے۔ یہ اسے استعمال کے لیے بہترین مواد بناتا ہے جو اعلیٰ سطح پر انحصار اور استحکام کا مطالبہ کرتا ہے۔
اسے دوبارہ لیپ اور پالش بھی کیا جا سکتا ہے تاکہ ایک مہر کو اس کی زندگی بھر میں کئی بار ری فربش کیا جا سکے۔ یہ عام طور پر زیادہ میکانکی طور پر استعمال ہوتا ہے، جیسا کہ مکینیکل مہروں میں اس کی اچھی کیمیائی سنکنرن مزاحمت، اعلی طاقت، اعلی سختی، اچھی لباس مزاحمت، چھوٹے رگڑ گتانک اور اعلی درجہ حرارت کی مزاحمت کے لیے۔
مکینیکل مہر کے چہروں کے لیے استعمال ہونے پر، سلکان کاربائیڈ کا نتیجہ بہتر کارکردگی، مہر کی زندگی میں اضافہ، دیکھ بھال کے کم اخراجات، اور گھومنے والے آلات جیسے ٹربائنز، کمپریسرز، اور سینٹری فیوگل پمپس کے لیے کم چلانے کے اخراجات کا نتیجہ ہوتا ہے۔ سلکان کاربائیڈ مختلف خصوصیات کے حامل ہو سکتے ہیں اس پر منحصر ہے کہ اسے کیسے بنایا گیا ہے۔ ری ایکشن بانڈڈ سلکان کاربائیڈ ایک رد عمل کے عمل میں سلکان کاربائیڈ کے ذرات کو ایک دوسرے سے جوڑ کر بنتا ہے۔
یہ عمل مواد کی زیادہ تر جسمانی اور حرارتی خصوصیات کو نمایاں طور پر متاثر نہیں کرتا، تاہم یہ مواد کی کیمیائی مزاحمت کو محدود کر دیتا ہے۔ سب سے عام کیمیکل جو ایک مسئلہ ہیں وہ ہیں کاسٹکس (اور دیگر اعلی پی ایچ کیمیکلز) اور مضبوط تیزاب، اور اس لیے ان ایپلی کیشنز کے ساتھ ری ایکشن بانڈڈ سلکان کاربائیڈ استعمال نہیں کرنا چاہیے۔
Reaction-sintered infiltratedسلکان کاربائیڈ. اس طرح کے مواد میں، دھاتی سلیکون کو جلا کر دراندازی کے عمل میں اصل SIC مواد کے سوراخ بھر جاتے ہیں، اس طرح ثانوی SiC ظاہر ہوتا ہے اور مواد غیر معمولی میکانکی خصوصیات حاصل کر لیتا ہے، جو لباس مزاحم بن جاتا ہے۔ اس کے کم سے کم سکڑنے کی وجہ سے، یہ قریبی رواداری کے ساتھ بڑے اور پیچیدہ حصوں کی پیداوار میں استعمال کیا جا سکتا ہے. تاہم، سلیکون مواد زیادہ سے زیادہ آپریٹنگ درجہ حرارت کو 1,350 °C تک محدود کرتا ہے، کیمیائی مزاحمت بھی تقریباً pH 10 تک محدود ہے۔ جارحانہ الکلین ماحول میں استعمال کے لیے مواد کی سفارش نہیں کی جاتی ہے۔
sinteredسلکان کاربائیڈ کو 2000 ° C کے درجہ حرارت پر پہلے سے کمپریسڈ بہت ہی باریک ایس آئی سی گرانولیٹ کو سنٹر کرکے حاصل کیا جاتا ہے تاکہ مواد کے دانوں کے درمیان مضبوط بانڈ بن سکے۔
سب سے پہلے، جالی گاڑھی ہوتی ہے، پھر پوروسیٹی کم ہوتی ہے، اور آخر میں دانوں کے درمیان بانڈز سنٹر ہوتے ہیں۔ اس طرح کی پروسیسنگ کے عمل میں، مصنوعات کا ایک اہم سکڑ جاتا ہے - تقریبا 20٪ تک.
SSIC مہر کی انگوٹی تمام کیمیکلز کے خلاف مزاحم ہے۔ چونکہ اس کی ساخت میں کوئی دھاتی سلکان موجود نہیں ہے، اس لیے اسے 1600C تک درجہ حرارت پر اس کی طاقت کو متاثر کیے بغیر استعمال کیا جا سکتا ہے۔
خواص | R-SiC | S-SiC |
پوروسیٹی (%) | ≤0.3 | ≤0.2 |
کثافت (g/cm3) | 3.05 | 3.1~3.15 |
سختی | 110~125 (HS) | 2800 (kg/mm2) |
لچکدار ماڈیولس (Gpa) | ≥400 | ≥410 |
SiC مواد (%) | ≥85% | ≥99% |
سی مواد (%) | ≤15% | 0.10% |
موڑنے کی طاقت (Mpa) | ≥350 | 450 |
دبانے والی طاقت (کلوگرام/ملی میٹر2) | ≥2200 | 3900 |
حرارت کی توسیع کا گتانک (1/℃) | 4.5×10-6 | 4.3×10-6 |
حرارت کی مزاحمت (ماحول میں) (℃) | 1300 | 1600 |
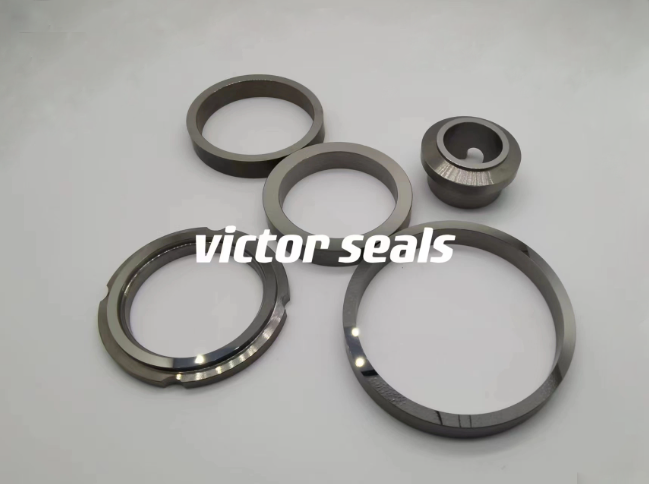
ٹی سی مکینیکل مہر
TC مواد میں اعلی سختی، طاقت، گھرشن مزاحمت اور سنکنرن مزاحمت کی خصوصیات ہیں۔ اسے "صنعتی دانت" کے نام سے جانا جاتا ہے۔ اس کی اعلی کارکردگی کی وجہ سے، یہ وسیع پیمانے پر فوجی صنعت، ایرو اسپیس، مکینیکل پروسیسنگ، دھات کاری، تیل کی کھدائی، الیکٹرانک مواصلات، فن تعمیر اور دیگر شعبوں میں استعمال کیا گیا ہے. مثال کے طور پر، پمپس، کمپریسرز اور ایگیٹیٹرز میں، ٹنگسٹن کاربائیڈ کی انگوٹھی کو مکینیکل سیل کے طور پر استعمال کیا جاتا ہے۔ اچھی رگڑ مزاحمت اور اعلی سختی اسے اعلی درجہ حرارت، رگڑ اور سنکنرن کے ساتھ لباس مزاحم حصوں کی تیاری کے لیے موزوں بناتی ہے۔
اس کی کیمیائی ساخت اور استعمال کی خصوصیات کے مطابق، TC کو چار اقسام میں تقسیم کیا جا سکتا ہے: ٹنگسٹن کوبالٹ (YG)، ٹنگسٹن-ٹائٹینیم (YT)، ٹنگسٹن ٹائٹینیم ٹینٹلم (YW)، اور ٹائٹینیم کاربائیڈ (YN)۔
ٹنگسٹن کوبالٹ (YG) ہارڈ الائے ڈبلیو سی اور کمپنی پر مشتمل ہے۔ یہ ٹوٹنے والے مواد جیسے کاسٹ آئرن، نان فیرس دھاتیں اور غیر دھاتی مواد کی پروسیسنگ کے لیے موزوں ہے۔
سٹیلائٹ (YT) WC، TiC اور Co پر مشتمل ہے۔ مرکب میں TiC شامل کرنے کی وجہ سے، اس کے پہننے کی مزاحمت بہتر ہوئی ہے، لیکن موڑنے کی طاقت، پیسنے کی کارکردگی اور تھرمل چالکتا میں کمی واقع ہوئی ہے۔ کم درجہ حرارت میں اس کی ٹوٹ پھوٹ کی وجہ سے، یہ صرف تیز رفتار کاٹنے والے عام مواد کے لیے موزوں ہے نہ کہ ٹوٹنے والے مواد کی پروسیسنگ کے لیے۔
ٹنگسٹن ٹائٹینیم ٹینٹلم (نیوبیم) کوبالٹ (وائی ڈبلیو) کو ٹینٹلم کاربائیڈ یا نیبیم کاربائیڈ کی مناسب مقدار کے ذریعے اعلی درجہ حرارت کی سختی، طاقت اور کھرچنے کی مزاحمت کو بڑھانے کے لیے ملاوٹ میں شامل کیا جاتا ہے۔ ایک ہی وقت میں، سختی کو بھی بہتر جامع کاٹنے کی کارکردگی کے ساتھ بہتر بنایا گیا ہے۔ یہ بنیادی طور پر سخت کاٹنے والے مواد اور وقفے وقفے سے کاٹنے کے لیے استعمال ہوتا ہے۔
کاربونائزڈ ٹائٹینیم بیس کلاس (YN) ایک سخت مرکب ہے جس میں TiC، نکل اور molybdenum کے سخت مرحلے ہیں۔ اس کے فوائد میں اعلی سختی، اینٹی بانڈنگ کی صلاحیت، اینٹی کریسنٹ پہننے اور اینٹی آکسیڈیشن کی صلاحیت ہے۔ 1000 ڈگری سے زیادہ درجہ حرارت پر، یہ اب بھی مشینی ہو سکتا ہے۔ یہ مصر دات اسٹیل اور بجھانے والے اسٹیل کی مستقل تکمیل پر لاگو ہوتا ہے۔
ماڈل | نکل کا مواد (wt%) | کثافت (g/cm²) | سختی (HRA) | موڑنے کی طاقت (≥N/mm²) |
YN6 | 5.7-6.2 | 14.5-14.9 | 88.5-91.0 | 1800 |
YN8 | 7.7-8.2 | 14.4-14.8 | 87.5-90.0 | 2000 |
ماڈل | کوبالٹ مواد (wt%) | کثافت (g/cm²) | سختی (HRA) | موڑنے کی طاقت (≥N/mm²) |
YG6 | 5.8-6.2 | 14.6-15.0 | 89.5-91.0 | 1800 |
YG8 | 7.8-8.2 | 14.5-14.9 | 88.0-90.5 | 1980 |
YG12 | 11.7-12.2 | 13.9-14.5 | 87.5-89.5 | 2400 |
YG15 | 14.6-15.2 | 13.9-14.2 | 87.5-89.0 | 2480 |
YG20 | 19.6-20.2 | 13.4-13.7 | 85.5-88.0 | 2650 |
YG25 | 24.5-25.2 | 12.9-13.2 | 84.5-87.5 | 2850 |